Rocky Mountain Institute
|
|
|
|
|
|
|
|
Certifications & Awards
Project Team
- Owner: Amory and Hunter Lovins
Green Building Audio
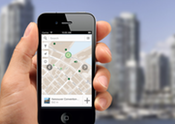
Our audio tours qualify.
Get one today!
Summary
Rocky Mountain Institute is located in the heart of the Old Snowmass Valley, a rural area 16 miles west of Aspen, Colorado.
**This building was originally imported from the U.S. Department of Energy Energy Efficiency and Renewable Energy
Building Technologies Database (http://eere.buildinggreen.com/overview.cfm?projectid=34) on 2009-06-06. Please confirm that the import was successful, login, and remove this message. Help make the Green Building Brain better.**
Overview
- Location: Snowmass, CO
- New construction
- 4,000 sq. feet (372 sq. meters)
- Project scope: a single building
- Rural setting
Completed 1984
Although the building was completed in 1984, it has been continuously updated and remains a showcase of energy-efficient design and construction techniques.
Rocky Mountain Institute is located in the heart of the Old Snowmass Valley, a rural area 16 miles west of Aspen, Colorado.
The original RMI building has three functions: a house for Amory and Hunter Lovins and their guests; a year-round growing space for fruits, vegetables, herbs, flowers, and fish; and a research center whose use is donated as the headquarters of RMI, a nonprofit resource policy center. It was designed by Steve Conger, AIA of the Aspen Design Group and constructed by Amory, Hunter, 12 professional builders and artisans, and over 100 volunteers.
Environmental Aspects
Energy and resource-efficient technologies are integrated with other elements such as natural lighting, good indoor air quality, plants, natural ventilation, and soothing sounds from a waterfall to produce a building that not only makes economic and environmental sense, but also makes people feel good.
Owner & Occupancy
- Owned and occupied by Amory and Hunter Lovins, Individual(s)
Keywords
Indigenous vegetation, Efficient fixtures and appliances, Massing and orientation, Insulation levels, Glazing, Airtightness, Passive solar, HVAC, Lighting control and daylight harvesting, Efficient lighting, On-site renewable electricity, Durability, Local materials, Daylighting, Noise control
Team & Process
Lawrence Doble Structural engineer Aspen, CO Jon Giltner, PE Nicol & Giltner Structural engineer Boulder, CO [Amory and Hunter Lovins](learnmore.cfm?ProjectID=34) Rocky Mountain Institute Owner/developer Snowmass, CO Steve Conger, AIA The Aspen Design Group Architect Aspen, CO Wright Water Engineers Water Engineers Glenwood Springs, COFinance & Cost
Cost data in U.S. dollars as of date of completion.
- Total project cost (land excluded): $500,000
RMI was built in 1984 for approximately $130/ft2 ($1,400/m2). (Building costs in Aspen, CO are nearly twice the national average.) In addition to high labor costs, a short building season, and the possibility of killing frosts at any time, non-native materials must be trucked over the Continental Divide.
After subtracting savings from avoiding the need for a furnace, the net additional cost of the RMI structure for energy and resource-efficient technologies was approximately $6,000.
The building produces an average of about $19 per day in saved energy. (In 1983, the energy savings repaid the extra cost of the efficient equipment in the first 10 months and will ultimately pay for the entire building in about 40 years.)
The electricity the building saves will avoid burning its own volume in coal every 20 years. (RMI saves electricity as well as heat; electricity is by far the costliest form of energy.)
RMI uses only 0.3 W/ft2 (3.2 W/m2) for power because it doesn't use electricity for space or water heating, air conditioning, cooking, clothes drying, or (most significantly) refrigeration. RMI uses power only for lights and small appliances, and its electric bill runs about $20 per month. In contrast, it's not uncommon for local all-electric houses of comparable size to incur a $1,000 per month winter electric bill.
RMI saves 99% of space and water heating energy, 90% of household electricity, and 50+% of household water compared to a typical house of comparable size.
Site Description
Water conservation is realized through the use of low-flow fixtures including showerheads that use 1.5-1.7 gal/min (5.7-6.4 L/min) of water and Swedish toilets that use 3-4 liters (0.8-1.1 gal) per flush.
Previously undeveloped land
Landscape Plantings
- Minimize turf area
Low-Water-Use Fixtures
- Install double-basin kitchen sinks
Siting Analysis
- Assess regional climatic conditions
Hot Water Delivery to Fixtures
- Design floorplan to minimize length of hot water piping
Site Planning
Site buildings so as to help occupants celebrate the natural beauty
- Provide for solar access
Energy
Lighting
Compact fluorescent lamps (CFLs) are used throughout RMI because each uses one-fourth the electricity of an incandescent bulb and lasts 10-13 times longer. Fluorescent lights in the computer room, kitchen, NE hall, and workshop use solid-state, high-frequency ballasts in place of conventional "core" ballasts. The solid-state ballasts last longer, eliminate flicker and hum, reduce electricity consumption by over 40%, reduce cooling loads in the summer, and repay their extra cost in about one year. Automatic dimming of the fluorescent lights increases the 40% energy savings from high-frequency ballasts to 70-90%.
Refrigeration
The RMI refrigerator is a 16 ft3 (0.45 m3) hybrid model using 5-7% of the electricity of a conventional refrigerator. It is so well-insulated that it uses less than 100 kWh per year instead of the usual 1,500 kWh per year (saving about $100 per year in electricity costs).
Photovoltaic Panels
Since May 1985, water heating has been almost entirely solar, from four PV panels on the roof.
At RMI, nearly all of the solar electricity generated is used in the building during the weekdays and displaces the need for utility power. However, on weekends and holidays, the surplus of electricity generated is sold back to the utility.
RMI's solar cells typically produce 20-33% of the total electricity used in the building, depending on the season and the weather. Solar cells of this capacity (approximately 2 kW in peak sunlight) provide much more electricity than is required to meet just household needs.
Passive Solar Design
RMI incorporated numerous solar design strategies, including a "passive clothes dryer." The dryer is actually a darkly painted closet or shaft rising to a clerestory where two small fans blow hot air down and around the vertically hung clothes. The solar dryer saves approximately 90% of the energy of a conventional dryer.
The bedroom wing is heated mainly by its south-facing windows. The living room and the research center receive spillover heat from the greenhouse. Sunlight enters through the many glazing areas and leaves via the vents in the back of the greenhouse arch. Extra heat is stored in the floor slabs and in the arch, floor, and contents of the greenhouse.
The greenhouse is a 900 ft2 (85 m2) area that sustains semitropical growing conditions year round. Plants, fish, and other creatures inhabit the area. From the two ponds for edible fish, water rich in nutrients fertilizes the greenhouse plants. Other fish-tank water is aerated by a waterfall (which also acoustically isolates the living area from the research area) and returned to the fish. The greenhouse arch serves several functions, including storing heat, diffusing light, supporting the roof beams, holding cooling vents, and collecting solar heat. The greenhouse arch collects hot air through two stacks that rise to just below the glass. Hot air is drawn into an air-to-air heat exchanger, a device that can recover up to 75% of the heat into fresh incoming air and route it to rooms that need heat. Heat stored in the mass of the arch preheats water in polybutylene piping going to the active solar system, reducing the necessary collector area by more than one-third.
Materials & Resources
A 4-in. (100 mm) layer of red-dyed concrete was poured over mesh and gravel on grade and steel-troweled. It contains coils of polybutylene pipe for solar radiant heating. The poured concrete floors are low-cost and low-maintenance.
Above the ceiling decking and beneath the EPDM roofing, a 3/8-in. (9.5 mm) base layer of freon (CFC)-filled polyurethane foam was covered with a polyethylene vapor barrier sealed to the wall insulation at its edges. Depending on the location, another 4-8 in. (100-200 mm) of polyurethane was installed beneath the EPDM. The foam and vapor barrier increases energy efficiency.
The EPDM roof was installed with a slope toward the roof drains. Immediately above the EPDM are: a layer of polyester "stonemat"; 4-5 in. (100-130 mm) of gravel; another layer of polyester "stonemat"; 6-8 in. (150-200 mm) of earth; and grass, wildflowers, and animals. The total design load on the roof is 250 lb/ft2 (12 kPa).
White plaster walls allow light to disperse widely throughout the building.
The 16-in.-thick (400 mm) walls consist of two 6-in. (150 mm) courses of masonry sandwiching 4 in. (100 mm) of freon (CFC)-filled polyurethane foam. The masonry walls are faced inside and out with more than 150 tons (136 tonnes) of thin Dakota sandstone rocks from a nearby mountain. The 16-in. (400 mm) walls and foam provide R-40 (RSI-7) insulation, not including doors and windows.
The heat mirror film between the two panes of glass in the windows traps heat inside the house. In addition, by blocking some infrared radiation, it helps to keep the greenhouse area from becoming overheated in the summer months. Argon (a cheap, inert gas) was injected into the window assembly to raise the heat-trapping value of the windows from about R-4.1 (RSI-0.7) to about R-5.3 (RSI-0.9).
Reusable Components
- Use materials with integral finish
Plan for Materials Longevity
- Select durable window assemblies
- Use materials and systems with low maintenance requirements
Transportation of Materials
Prefer materials that are sourced and manufactured within the local area
Indoor Environment
The computer room lighting fixtures use radial polarizing lenses to cut veiling glare, allowing occupants to read computer screens and paper with greater contrast in less light. Fluorescent lights in the computer room, kitchen, NE hall, and workshop are solid-state, high-frequency ballasts, which have no flicker or hum. The brightness throughout the structure is created by the penetration of low winter sun to the back of the north wall; heat and light are not concentrated on the south side but dispersed to the north side of the building. Natural ventilation, plants, and an indoor waterfall enhance indoor environmental quality at RMI.
Outdoor Pollution Sources
- Locate building away from sources of pollution
Visual Comfort and The Building Envelope
Use large exterior windows and high ceilings to increase daylighting
Visual Comfort and Interior Design
Use low partitions near the exterior glazing to promote daylight penetration
- Place primarily unoccupied spaces away from daylight sources
Visual Comfort and Light Sources
- Use electronic ballasts with fluorescent lighting
- Provide illumination sensors
Direct Exhaust from High-source Locations
Use special equipment for ventilating locations with high heat loads
- Ensure that kitchen range hoods exhaust to the outdoors
Above Grade Humidity and Condensation
Use windows that provide R-3 or better over their entire surface
Reduction of Indoor Pollutants
- Avoid adhering carpet directly to concrete floor
Lessons Learned
The coordination of diverse volunteers and professionals as well as donated materials added complexity to this project's construction. The overall goal of energy efficiency with both technological and natural solutions was a focal point of the design and construction of this structure. Due to the difficulties associated with building in a remote area, materials were kept basic and local. Financial considerations as well as environmental impact assessments were balanced.
RMI continues to be a resource center for many energy-efficient approaches to our built environment; workbooks, publications, and CDs are available through RMI covering community resourcefulness, green development, and residential energy savings. The building itself serves as a symbol of the Institute's goals and is often cited as an example of the possibilities for energy-conserving design in cold climates. Due to an increase in the number of Institute employees, RMI has expanded into nearby office space.
Learn More
It is possible to visit this project and tours are available. Rocky Mountain Institute's Headquarters Building is located in Old Snowmass, Colorado, 14 miles northwest of the Aspen airport.
For details, download a map and directions (PDF-34K) to RMI from either Aspen or Glenwood Sprigs.
Free, hour-long, guided tours are conducted on Fridays (excepting holidays) at 2:00 p.m. Visitors can also take self-guided tours during regular business hours (9:00 a.m. to 4:30 p.m., Monday through Friday).
For large groups, advance arrangements are required. Please contact [email protected] if your group will number more than six or if you are bringng a group of students.
Web sites
Rocky Mountain Institute Website
Rocky Mountain Institute's Website includes a description of the Headquarters Building, but also a great deal of information on RMI's research and advocacy work.