Langara Science and Technology Building
Certifications & Awards
Project Team
- Building Envelope Consultant: Read Jones Christofferson Ltd.
- Civil Consultant: Aplin & Martin Consultants Inc.
- Electrical Consultant: AES Engineering Ltd.
- LEED Consultant : ZON Engineering
- Mechanical Specialty Consultant: TC Thermenex Inc.
- Mechanical Consultant: AME Consulting Group Ltd.
- Structural Consultant: Weiler Smith Bowers Consulting Structural Engineers
- General Contractors: Bird Construction
- Architects: Teeple Architects/Proscenium Architecture + Interiors Inc.
- Owner: Langara College
Green Building Audio
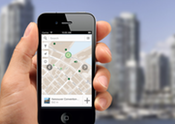
Our audio tours qualify.
Get one today!
Langara Science and Technology Building - Wendy Lannard, Facilities Director, Langara College & Kori Chan, partner architect at Proscenium Architecture + Interiors
Summary
The Science & Technology Building features over 12,000 square metres of new campus space allocated over five storeys. On the west side, a dramatic 16-metre cantilevered portion incorporates a skylight window that allows natural daylight to penetrate through to the ground below. Registrar & Enrolment Services and food outlets anchor the main floor, with event space and meeting rooms on the second level. State-of-the-art chemistry, biology, physics, astronomy, nursing, and computing science labs populate the upper three floors. There are also collaborative study spaces, a greenhouse for instructional purposes, and an observation deck on the roof. The new building is pursuing 3rd party certification via the Canada Green Building Council, aiming for a Gold level in their Leadership in Energy and Environment Design (LEED) standard. The project has incorporated green building features such as a low emissivity roof, the use of local, sustainable building materials, an energy-efficient building envelope, and low-flow fume hoods with adjustable sashes.
Green Building Highlighted Features
- Proximity to major transportation hubs
- Protected a landscaped area from future development equal to the building footprint (2087 m2)
- Modeled to save the equivalent of an Olympic swimming pool of water each year through washroom fixture efficiencies
- Innovative water-side heat recovery system that targets zero thermal energy waste and preheats domestic hot water
- Outdoor views in over 90% of the regularly occupied areas for greater indoor environment quality
Sustainable Sites
The Langara College Science & Technology Building project is located about 430 meters from the Langara-49th Skytrain station, which is less than a 4-minute walk. The Canada Line rapid transit rail runs from Vancouver to Richmond with a service frequency of 6-7 minutes in both directions at peak times of the day. Proximity to this rail line as well as frequent bus service along 49th Avenue creates ease in transit commuting to the Langara campus, delivering a high potential for reducing single-occupant vehicle demand. The campus is also located close to a major north-south cycling route on Ontario Street.
Langara incorporated a number of additional strategies on site to encourage sustainable transportation. End-of-trip change rooms and secure bike storage facilities for 5% of the building occupants create an accommodating atmosphere for cycle commuters. Electric vehicle recharging stations are located in a preferred parking area to accommodate 3% of building occupants. For building users who carpool, there are preferred parking spots as well as a program to encourage this method of single occupant vehicle demand reduction. The parking area itself is less than 3.5 spaces per 93 m2 (1000 sft) and does not exceed local zoning requirements.
The project site incorporated additional innovative design elements to promote walking, cycling and other non-motorized transportation on the site and within the surrounding community to reduce vehicle miles traveled, increase public health and enhance community participation.
This project incorporated a number of efforts to ensure site development impacts were lower than that of a conventional building. Building sites typically have a lot of asphalt parking areas or dark-coloured hardscaped areas. In the interest of mitigating the negative heat island effect that comes from the resultant higher temperature microclimates, the project opted for lighter, more reflective hardscaping surfaces, known as high albedo or low-emissive materials. Portions of these hardscape surfaces are also shaded by the roof and overhang areas for heat island effect prevention.
A large portion of landscaped area has been protected from future development. This greenspace, which is equal to the area of the building’s footprint (2087 m2), serves as type of offset for the building in an effort to conserve existing natural areas, provide habitat and promote biodiversity.
Water efficient landscaping
To promote a low-impact landscape plan, native and drought-tolerant plants were selected, including a sod mix of predominantly Fescue and Ryegrass. Fescue grass is a drought-tolerant alternative to traditional Kentucky Bluegrass and precludes the need for an on-site irrigation system. The sod may turn yellow to brown in drought conditions, however, Langara has committed to no irrigation as a way to conserve potable water.
Indoor water efficiency
The project created a model estimate of its indoor water use for plumbing fixtures and found the Science and Technology Building could save over a million litres (over 264 gallons) of potable water a year by specifying low flow fixtures with aerators for additional efficiencies. This 44% modeled savings in water is equal to an Olympic swimming pool of water each year. The building installed a whole building water meter to continue to measure and manage its consumption.
Materials & Resources
The use of building materials originating from local sources lowers the transport-related carbon footprint of the building while also supporting regional economies. Materials manufactured and harvested and extracted within regional distances were specified wherever possible, as well as products made with recycled materials.
The construction team prioritized the responsible management of construction waste through minimizing materials sent to the landfill as much as possible, with a minimum target of 2/3 material waste diversion.
Energy Performance
Green buildings work as an entire system to ensure energy conversation measures work together. The most energy efficient mechanical systems won’t make a difference in overall energy savings if installed in a building with poor insulation or with a leaky air barrier.
The design and construction team worked with a building envelope scientist to create a building durability plan to ensure the material selection, details, connections and interactions of the project’s assembly all work as a coherent building enclosure system for maximum longevity. High levels of insulation in the walls and roofs and high performance windows with low-e coatings ensure the building’s mechanical systems do not have to work as hard to keep the occupants comfortable regardless of weather conditions.
The primary source of heat for the building is provided from heat recovery modular chillers located on the roof, with back up boilers. Heat recovery coils also provide exhaust air streams, which recover heat and contribute to the heating load of the building.
The building uses a water-side heat recovery system. The central cooling plant consists of these water-cooled heat recovery chillers and a cooling tower. The majority of the heat rejected from the chillers is injected back into the heating system through a Thermenex header.
Thermenex technology uses a water-filled pipe that functions as a hub for thermal energy exchange. This long length of pipe has a temperature differential from one end to the other. Best described as a “thermal gradient header” (TGH), water can flow in either direction, and the secondary pumps then distribute and reclaimed heat or chilled water at optimal temperatures throughout the building, ensuring zones are provided with the ideal water temperature to meet demand. Heating and cooling can be added for peak demand, if needed. The benefit of using a thermal gradient header pipe for heating and cooling is it allows all heating loads to be considered as cooling sources and all cooling loads as heat sources, thereby targeting zero thermal energy waste. The Thermenex header also preheats domestic hot water from reclaimed heat within the building, with boilers providing the final heat of domestic hot water. The building has three air-handling units to deliver the right amount of ventilation to meet the high quality ASHRAE standards, which are based on occupancy and floor area. Scheduling the heating and cooling based on occupancy makes a lot of sense as it can lead to a more efficiently run system. Each zone in the building has a variable air volume (VAV) box with reheat coils to further control the air supply based on occupancy and schedule. When the space is unoccupied, the VAV box will close, for optimal energy savings.
The air-handling units themselves have variable speed drives. These minimize the volume of outside air that is required to be heated, and reduces the heating loads and therefore the amount of energy used during the heating season. They also reduce wear and tear on the unit fans and allow maximum energy savings.
Heat is recovered from lab exhaust fans, washrooms, and non-grease kitchens and injected back into the Thermenex header before the exhaust air leaves the building.
Indoor Environmental Quality
The harvesting of daylight is a multiple benefit strategy in a green building such as this. Not only do occupants enjoy a more pleasant indoor environment with quality daylight illuminating their tasks, but daylight also provides an important energy conversation strategy. Whenever there is enough daylight illumination, interior lighting is reduced or turned off with automatic daylight controls managing the balance between artificial and natural light.
In the interest of creating even further connection with the outdoor environment, the Science & Technology Building was designed to provide occupants with exterior views throughout the majority of the building. Over 90% of the regularly occupied areas of the building have been provided with views, with interior partitions constructed with full height glazing to optimize views for occupants working in non-perimeter spaces.
The air quality of indoor spaces was safeguarded during the construction process through the specification and installation of low-emitting paints, coatings, adhesives and sealants. Attention was also given to flooring emission standards, ensuring it met the FloorScore IAQ Test Program
Langara has committed to maintaining and operating the Science and Technology building in an ecologically sensitive manner. Toward this end, a Green maintenance and cleaning program ensures cleaning products and procedures protect the respiratory health of occupants through chemical reduction, the championing of Green Seal and EcoLogo certified products, policy and training.
To care for the landscaped areas, green landscaping practices have been put into policy and practice to ensure, for instance, that fertilizers are free of phosphates. Hardscape and building exterior maintenance policies have been put in place to minimize environmental impacts, such as low-VOC paints, environmentally sensitive equipment and low-impact snow and ice removal.
All of the above features and the architectural virtues make this building a landmark of pride on the Langara campus.
Sources http://www.canadianconsultingengineer.com/features/thermenex-at-langara/