Jones Federal Building and Courthouse
|
|
|
|
|
|
|
|
|
|
|
Certifications & Awards
- LEED-NC v.2/v.2.1 in 2002 achievement level Certified (27 points)
Project Team
- Owner: General Services Administration
Green Building Audio
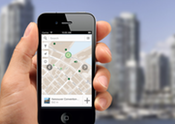
Our audio tours qualify.
Get one today!
Summary
The Nathaniel R. Jones Federal Building and U.S. Courthouse in Youngstown, Ohio, houses not only the U.S. Bankruptcy Court, but also various federal offices. The project team accommodated the sometimes conflicting requirements of the diverse tenant agencies while maintaining a commitment to security and green design.
**This building was originally imported from the U.S. Department of Energy Energy Efficiency and Renewable Energy
Building Technologies Database (http://eere.buildinggreen.com/overview.cfm?projectid=339) on 2009-06-06. Please confirm that the import was successful, login, and remove this message. Help make the Green Building Brain better.**
Overview
- Location: Youngstown, OH
- Building type(s): Public order & safety
- New construction
- 52,200 sq. feet (4,850 sq. meters)
- Project scope: 4-story building
- Urban setting
- Completed September 2002
Rating: U.S. Green Building Council LEED-NC, v.2/v.2.1--Level: Certified (27 points)
The Nathaniel R. Jones Federal Building and U.S. Courthouse in Youngstown, Ohio, houses not only the U.S. Bankruptcy Court, but also various federal offices. The project team accommodated the sometimes conflicting requirements of the diverse tenant agencies while maintaining a commitment to security and green design.
Environmental Aspects
The building was the first courthouse completed by the U.S. General Services Administration (GSA) to receive Leadership in Energy and Environmental Design (LEED) certification from the U.S. Green Building Council. Both the LEED Rating System and the GSA Construction Excellence Program drove the design and construction process, allowing green building principles and best construction practices to be integrated into the project.
Built on an urban brownfield site, the facility was designed to contribute to the revitalization of downtown Youngstown. A previously paved portion of the site was converted to greenspace, significantly reducing the site's impervious area. Reflective roofing and the use of concrete instead of asphalt parking-lot paving reduce the project's contribution to the urban heat-island effect.
More than 70% of the total construction debris, by weight, was recycled; soil and old concrete foundation materials were excavated and used for site grading. More than 60% of the building materials used, by cost, were sourced or manufactured locally. Recycled content materials included carpeting and structural steel.
The building was designed to be energy efficient, using extensive daylighting, spectrally selective glazing, and photoelectric sensors to minimize electricity use for lighting. Several post-occupancy adjustments, including the installation of a recirculation loop in the heating system and personnel training, reduced consumption by an additional 20 to 25%.
Owner & Occupancy
Owned and occupied by General Services Administration, Federal government
Typically occupied by 45 people, 40 hours per person per week; and 600 visitors per week, 2 hours per visitor per week
Building Programs
Indoor Spaces: | Office, Structured parking, Lobby/reception, Mechanical systems, Other |
Outdoor Spaces: | Restored landscape, Parking |
Keywords
Integrated team, Design charrette, Commissioning, Brownfield redevelopment, Drought-tolerant landscaping, Lighting control and daylight harvesting, Recycled materials, Local materials, C&D waste management, Occupant recycling, Daylighting, Low-emitting materials
Team & Process
The need for a new building resulted from growth of federal courts' needs and limited space in the existing Thomas D. Lambros Federal Building and U.S. Courthouse, located in downtown Youngstown. Key priorities included ensuring close proximity to the Lambros building, which the new building would complement; remaining within the Youngstown central business district to support city revitalization; and projecting an architectural image for the federal justice system that conveys openness and dignity.
A newly established Construction Excellence Program by the U.S. General Services Administration (GSA) guided project goals toward low construction costs, high efficiencies, and value enhancement. One major value enhancement was using the building for multiple occupancies, including other federal tenants. Providing building security, an important consideration in the planning stages, was complicated by the mixed occupancy.
Other project goals were to complete the project within a tight budget, meet the construction schedule, and adopt green building principles in the planning process.
A one-day design charrette held during the project development stage allowed team members to interact and collaborate. Team members established sustainable design criteria and decided to use the LEED(r) Rating System. LEED certification was not mandatory for federal buildings at this time; however, the team determined that certification would benefit the project and provide valuable experience for future federal projects. During subsequent design discussions, green design became a top priority and helped bring the divergent elements of the project together.
GSA used the Construction Manager as Constructor (CMc) project delivery method, with a pre-established, guaranteed maximum price. In this arrangement, the CMc firm provided design reviews, cost estimates, scheduling, and other services, in addition to the basic construction of the building.
The building is primarily steel frame construction, with some masonry at the lower level. The exterior is clad with brick, cast stone, and a glass and aluminum curtain wall.
The project team completed the facility on schedule and within budget.
A building automation system controls and monitors building systems.
The project engineering firm commissioned the building for LEED certification.
Post-occupancy evaluations, including an energy audit, revealed the need for building systems optimization and additional personnel training. Adjustments that were made after occupancy reduced energy use by over 20%.
[Grant Marani](learnmore.cfm?ProjectID=339) Robert A.M. Stern Architects Architect New York, NY [http://www.ramsa.com](http://www.ramsa.com) [Pam Wilczynski](learnmore.cfm?ProjectID=339) U.S. General Services Administration Project manager Chicago, IL Ron Cortes Dick Corporation Contractor Pittsburgh, PA [http://www.dickcorp.com](http://www.dickcorp.com) John Roush URS Corporation Mechanical and structural engineer Cleveland, OH [http://www.urscorp.com](http://www.urscorp.com) Gregg Calpino SmithGroup JJR Landscape architect Chicago, IL [http://www.jjr-us.com](http://www.jjr-us.com)Finance & Cost
In addition to the government appropriations for the project, the U.S. Department of Energy's Federal Energy Management Program provided $18,402 in grant funding to offset a portion of the commissioning and LEED documentation costs.
- Equity: Government appropriation
- Grant: Public agency
Cost data in U.S. dollars as of date of completion.
- Total project cost (land excluded): $17,856,755
Soft cost: $39 per sq foot ($420 per sq meter)
- professional fee: $22 per sq foot ($240 per sq meter)
- management fee: $16 per sq foot ($170 per sq meter)
Hard cost: $302 per sq foot ($3,250 per sq meter)
- site work: $30 per sq foot ($300 per sq meter)
- construction: $239 per sq foot ($2,570 per sq meter)
- tenant improvements: $32 per sq foot ($340 per sq meter)
Land Use & Community
The project site is a redeveloped urban brownfield. Access to the site via public transportation is limited. The building has five parking spaces in the lower-level garage and 72 spaces in the outside lot.
Properties with Excessive Impacts
- Avoid contributing to sprawl
Property Selection Opportunities
- Select brownfield sites for development
Site Description
The building is located on a brownfield site. Soil stabilization measures included considerable site regrading. A 1.8-acre previously paved portion of the site was converted to greenspace with climate-adapted, drought-tolerant plant species. The completed site has 58% less impervious surface than the original site. Earth and foundation materials excavated from the site, including approximately 300 tons of crushed concrete, were used to regrade the site. Light-colored concrete was used in place of asphalt for the majority of newly poured paving to reduce the project's contribution to the urban heat-island effect.
- Lot size: 3.09 acres
- Building footprint: 13,700 sq ft (1,270 sq meters)
- Brownfield site
Water Conservation and Use
The site is landscaped with drought-tolerant plant species, and no irrigation systems were planned or installed. Water conservation measures will save an estimated one million gallons of water annually.
Water Use
-
**Remediation of Damaged Sites**
-
Investigate government programs to assist in remediating brownfield
sites
- Decontaminate brownfield sites
Demand for Irrigation
- Select plants for drought tolerance
Integration with Site Resources
- Use light-colored pavement to reduce heat island effect
Low-Impact Siting
- Look for opportunities to combine needs with infrastructure
Select building sites that make use of existing infrastructure
Energy
Heat, supplied by municipal utility steam, is distributed via coil-equipped air handlers and finned-tube radiators. Originally, chilled water for cooling was also to be supplied by the utility; however, late in the project, the chilled water became unavailable, and, instead, air-cooled chillers, with an approximate total capacity of 200 tons, were installed on site. This unexpected change resulted in an additional cost of approximately $80,000.
Several adjustments made after occupancy improved the building's energy efficiency. Excessive run time in the chillers was discovered and attributed to heat gain in the computer equipment rooms. A packaged cooling unit was then installed in each of the three computer rooms to handle this localized cooling load. This allowed the main chillers to handle the general building cooling loads. Exhaust heat from the packaged coolers is directed to the lower-level parking garage. A recirculation loop was installed to optimize the use of the utility supplied heat. As a result of these efforts, as well as adjustments to building system controls, the overall energy consumption was reduced by 20 to 25%.
Clerestory windows, a central light well, and conventional windows supply daylighting to over 75% of occupied spaces. Spectrally selective glazing in all of the fenestration controls excess heat gain while transmitting high levels of visible light. Photoelectric sensors dim or turn off electric lights when daylight is sufficient. A highly reflective, white membrane roof reduces heat gain during the cooling season. (A small portion of the roof is metal.)
Materials & Resources
An estimated 62% of the building materials used, by cost, were sourced or manufactured within 500 miles of the site. Locally sourced brick veneer, for example, was used on a portion of the building exterior.
Steel used for the building's structural frame has a recycled content of approximately 90%, including substantial post-consumer content. The carpeting used in the building also has recycled content.
Ozone-safe compounds were specified as fire suppressant, and an ozone-safe refrigerant is used in the chillers.
A recycling station is provided for occupant use.
Concrete and over 12.5 tons of steel were separated from the waste stream and recycled. According to hauler receipts and other documentation, 72% of the total construction debris, by weight, was recycled.
Because the building contains a courtroom, with specialized functional and security features, the potential for future reuse is limited. As a part of the site planning process, however, consideration was given to future expansion by determining a location for an annex addition to the building.
Job Site Recycling
- Set up labeled bins to keep recyclable materials separate
Recycling by Occupants
Specify recycling receptacles that are accessible to the occupants
Post-Consumer Recycled Materials
- Specify heavy steel framing with highest recycled content
Transportation of Materials
Prefer materials that are sourced and manufactured within the local area
Indoor Environment
Over 75% of the occupied building spaces are daylit. During construction, ducts were sealed to prevent the entry of dust and other contaminants. For a two-week period prior to occupancy, the building was ventilated to purge residual airborne pollutants. The carpeting and wood composites used in the building have low levels of volatile organic compound (VOC) emissions.
Visual Comfort and The Building Envelope
Use large exterior windows and high ceilings to increase daylighting
Identification of Indoor Pollutants
- Procure green-label-certified carpet
Ventilation During Construction
Purge the building of VOCs during furniture installation prior to move-in
Facility Policies for IEQ
- Recommend a non-smoking policy for the building
Awards
White House Closing the Circle Award in 2003; Category/title: Sustainable Design/Green Buildings
Ratings
U.S. Green Building Council LEED-NC, v.2/v.2.1 in 2002; achievement level: Certified (27 points)
Sustainable Sites, 10 of 14 possible points
- SS Prerequisite 1, Erosion & Sedimentation Control
- SS Credit 1, Site Selection
- SS Credit 2, Urban Redevelopment
- SS Credit 3, Brownfield Redevelopment
SS Credit 4.1, Alternative Transportation, Public Transportation Access
SS Credit 5.1, Reduced Site Disturbance, Protect or Restore Open Space
- SS Credit 5.2, Reduced Site Disturbance, Development Footprint
- SS Credit 6.1, Stormwater Management, Rate and Quantity
SS Credit 7.1, Landscape & Exterior Design to Reduce Heat Islands, Non-Roof
SS Credit 7.2, Landscape & Exterior Design to Reduce Heat Islands, Roof
- SS Credit 8, Light Pollution Reduction
Water Efficiency, 2 of 5 possible points
- WE Credit 1.1, Water Efficient Landscaping, Reduce by 50%
WE Credit 1.2, Water Efficient Landscaping, No Potable Water Use or No Irrigation
Energy and Atmosphere, 1 of 17 possible points
- EA Prerequisite 1, Fundamental Building Systems Commissioning
- EA Prerequisite 2, Minimum Energy Performance
- EA Prerequisite 3, CFC Reduction in HVAC&R Equipment
- EA Credit 4, Ozone Depletion
Materials and Resources, 4 of 13 possible points
- MR Prerequisite 1, Storage & Collection of Recyclables
- MR Credit 2.1, Construction Waste Management, Divert 50%
MR Credit 4.1, Recycled Content: 5% (post-consumer + 1/2 post-industrial)
MR Credit 4.2, Recycled Content: 10% (post-consumer + 1/2 post-industrial)
MR Credit 5.1, Local/Regional Materials, 20% Manufactured Locally
Indoor Environmental Quality, 8 of 15 possible points
- EQ Prerequisite 1, Minimum IAQ Performance
- EQ Prerequisite 2, Environmental Tobacco Smoke (ETS) Control
- EQ Credit 1, Carbon Dioxide (CO2) Monitoring
EQ Credit 3.1, Construction IAQ Management Plan, During Construction
EQ Credit 3.2, Construction IAQ Management Plan, Before Occupancy
- EQ Credit 4.1, Low-Emitting Materials, Adhesives & Sealants
- EQ Credit 4.3, Low-Emitting Materials, Carpet
- EQ Credit 4.4, Low-Emitting Materials, Composite Wood
- EQ Credit 8.1, Daylight & Views, Daylight 75% of Spaces
- EQ Credit 8.2, Daylight & Views, Views for 90% of Spaces
Innovation and Design Process, 2 of 5 possible points
ID Credit 1.1, Innovation in Design "Exemplary Local Materials, Over 60%"
- ID Credit 2, LEED® Accredited Professional
Lessons Learned
The budgetary and completion date targets for this building were not only met, but exceeded. An outside, independent scheduler provided ongoing schedule analysis, evaluated progress, and anticipated delays. The scheduler identified at least one major bottleneck and worked with the project team to avert what could have been a serious delay.
Because this was the first GSA project of its type to achieve LEED certification, initial estimates of costs for meeting LEED criteria were too high. This nearly led to abandoning LEED sustainable design principles, which seemed too costly to keep the project within budget.
The design team originally sought a LEED rating higher than basic certification. In some cases, credits were not achieved due to lack of documentation, insufficient monitoring, lack of readily deliverable materials, or misunderstandings about credit requirements.
Early in the operation of the building, energy consumption was found to be significantly higher than projected. Commissioning turned up several causes, including high internal heat gain in the computer rooms. Building systems were optimized, and training for operating personnel increased their familiarity with building systems and controls. A comprehensive energy audit was also done so that building performance could be optimized or corrected to meet original design goals.
Learn More
It is possible to visit this project. The Nathaniel R. Jones U.S. Courthouse is located at 100 East Commerce Street in Youngstown, Ohio.
Web sites
Federal Building - U. S. Courthouse: Youngstown, OH
This website provides general information about the project and photographs of the site during construction.Frank J. Battisti and Nathaniel R. Jones Federal Building and U.S. Courthouse, Youngstown, OH General Services Administration
A brief case study describing the basic features of the building.
Others
Booklet: Federal Building United States Courthouse: Youngstown, Ohio (October 2002)
This government-published booklet provides a basic description of the building, complete with photographs.Report: Sustainable Design in Federal Facilities (August 2003)
This document includes a brief case study of the project. (PDF 712 KB) Download Acrobat Reader