Hawaii Gateway Energy Center
|
|
|
|
|
|
|
|
|
|
|
|
|
|
|
|
Certifications & Awards
- LEED-NC v.2/v.2.1 in 2005 achievement level Platinum (52 points)
- Zero Energy Building
Project Team
- Owner: Natural Energy Laboratory of Hawaii Authority (NELHA)
Green Building Audio
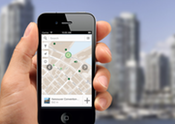
Our audio tours qualify.
Get one today!
Summary
The Hawaii Gateway Energy Center (HGEC) visitor complex, situated on the south coast of Kona on the Big Island of Hawaii, serves the Natural Energy Laboratory of Hawaii (NELH). It is the first building to be constructed on a 6.5 acre campus designed to house research, development, and demonstration facilities for energy and technological fields. The NELH facilities are run by the State of Hawaii under the Natural Energy Laboratory of Hawaii Authority (NELHA).
**This building was originally imported from the U.S. Department of Energy Energy Efficiency and Renewable Energy
Building Technologies Database (http://eere.buildinggreen.com/overview.cfm?projectid=592) on 2009-06-06. Please confirm that the import was successful, login, and remove this message. Help make the Green Building Brain better.**
Overview
- Location: Kailua-Kona, HI
Building type(s): Other, Assembly, Commercial office, Interpretive Center
- New construction
- 3,600 sq. feet (334 sq. meters)
- Urban setting
- Completed January 2005
Rating: U.S. Green Building Council LEED-NC, v.2/v.2.1--Level: Platinum (52 points)
Rating: Zero Energy Building
The Hawaii Gateway Energy Center (HGEC) visitor complex, situated on the south coast of Kona on the Big Island of Hawaii, serves the Natural Energy Laboratory of Hawaii (NELH). It is the first building to be constructed on a 6.5 acre campus designed to house research, development, and demonstration facilities for energy and technological fields. The NELH facilities are run by the State of Hawaii under the Natural Energy Laboratory of Hawaii Authority (NELHA).
The visitor complex houses administrative office space, restrooms, support areas, and a large multi-purpose space that will be used for displays, outreach, conferencing, and education. The first phase of the plan for the site also includes a small research laboratory facility. The second phase will add more laboratory space to complete the campus.
Environmental Aspects
HGEC is designed as a thermal chimney, capturing heat and creating air movement using only building form and thermodynamic principles. Outside air is moved through the building at a rate of 10 to 15 air changes per hour without the use of a mechanical system.
The copper roof radiates heat from the sun into a ceiling plenum; the heated air rises and is exhausted through stacks on the building's north face. As the hot air is exhausted, fresh outside air is pulled into the occupied space from a vented underfloor plenum. Incoming air is drawn across cooling coils filled with 45°F seawater and cooled to 72°F. Condensation collected below the seawater cooling coils is used for flushing toilets and irrigating deep-rooted landscaping.
The building orientation and configuration allow daylighting to eliminate the need for electric lighting during daylight hours. All glazing is shaded to prevent direct solar gain.
The building was designed with an onsite, 20-kilowatt photovoltaic array. When the building was constructed, this provided about half of the total energy needed to run the seawater pumps, lights, and other electrical equipment. A pump adjustment in 2006 means that the photovoltaic system now provides all of the energy needed on site.
Owner & Occupancy
Owned and occupied by Natural Energy Laboratory of Hawaii Authority (NELHA), State government
Typically occupied by 4 people, 40 hours per person per week; and 300 visitors per week, 2 hours per visitor per week
Building Programs
Indoor Spaces: | Conference (67%), Office (33%), Public assembly, Restrooms |
Outdoor Spaces: | Parking, Restored landscape, Drives/roadway, Patio/hardscape, Interpretive landscape |
Keywords
Integrated team, Design charrette, Green framework, Simulation, Green specifications, Commissioning, Performance measurement and verification, Operations and maintenance, Indigenous vegetation, Stormwater management, Water harvesting, Efficient fixtures and appliances, Efficient irrigation, Graywater, Massing and orientation, Insulation levels, Glazing, Airtightness, Passive solar, Lighting control and daylight harvesting, Efficient lighting, On-site renewable electricity, Durability, Benign materials, Recycled materials, Local materials, C&D waste management, Occupant recycling, Connection to outdoors, Daylighting, Natural ventilation, Ventilation effectiveness, Moisture control, Thermal comfort, Noise control, Low-emitting materials, Indoor air quality monitoring
Team & Process
The initial request for proposals for the Hawaii Gateway Energy Center called for a zero-net-energy facility that would incorporate green building strategies and demonstrate the unique resources and mission of the Natural Energy Laboratory of Hawaii Authority (NELHA).
In the predesign phase, the design team established strategies to put the principles into practice and defined the degree of innovation that NELHA would consider. While making these decisions, the team shifted from imagining a vague idea of sustainability to targeting state-of-the-art green design. At this point, the team agreed to attempt LEED(r) Platinum certification even though LEED certification was not a requirement of the initial request for proposals.
With the support of the client, the architecture and engineering team envisioned a facility that would merit national and international recognition while contributing to the local community. The client played an integral part in planning and imaging sessions and fully supported the team's decision to pursue unconventional passive design strategies.
During the predesign phase, the client established beneficial partnerships with the local electric utility (Hawaii Electric Light Company) and land-use planning authority, both of whom took extraordinary interest in the long-term implications of the renewable energy, energy distribution, and water conservation technologies that HGEC would demonstrate.
The unconventional design phase utilized a "whole design process," which differed from a "linear design process" in that the architect and the consultants worked in concert from the beginning, evolving the design as a team. This approach was critical to the successful integration of the passive design strategies, including daylighting, induced ventilation, passive cooling, and condensation irrigation.
The project team envisioned designing the building as a thermal chimney to induce ventilation. The team identified solar radiation as the "engine" that, simply by the laws of thermodynamics, would move ventilation air without need for electric fans. Cold, deep seawater available on the site would provide free cooling (except for the pump energy needed to circulate the seawater through the cooling coils).
To ensure that the building would function passively as an effective thermal chimney, the team performed sophisticated computer modeling. This established the building geometry and free area requirements along the ventilation pathway from the exterior inlets, below-floor plenum, ceiling plenum, and chimney outlets that were maintained throughout the design. Computer analysis also verified the effectiveness of daylighting and shading design strategies.
A waste management plan and indoor air quality management plan were implemented during construction. Additionally, site disruption and erosion were minimized.
Owner training was included in the commissioning process. The extensive use of passive design and low-maintenance materials should result in minimal maintenance requirements.
Both fundamental and additional commissioning were implemented on this project.
In 2006, refinements to seawater pump flow and pressure have resulted in substantial improvements in building performance; the building is now a net-exporter of energy.
Natural Energy Laboratory of Hawaii Authority Owner/developer Kailua-Kona, HI [http://www.nelha.org](http://www.nelha.org) Ferraro Choi And Associates, Ltd. Architect Honolulu, HI [www.ferrarochoi.com](www.ferrarochoi.com) RM Towill Corporation Civil engineer Kailua-Kona, HI [http://www.rmtowill.com](http://www.rmtowill.com) Libbey Heywood, Inc. Structural engineer Honolulu, HI [http://www.lhise.com](http://www.lhise.com) Lincolne Scott, Inc. MEP engineer, lighting and energy consultant Honolulu, HI [http://www.lincolnescott.com](http://www.lincolnescott.com) LP&D Hawaii Landscape architect Honolulu, HI ENSAR Group, Inc. (now RMI/ENSAR Built Environment) LEED management Boulder, CO [http://www.ensargroup.com](http://www.ensargroup.com) Engineering Economics, Inc. Commissioning agent Golden, CO [http://www.eeiengineers.com/](http://www.eeiengineers.com/) Bolton, Inc. Contractor Kailua-Kona, HI Triodetic Space Frames, Inc. Space frames Syracuse, NY [William Brooks, AIA](learnmore.cfm?ProjectID=592) Ferraro Choi And Associates, Ltd. Architect Honolulu, HI [http://www.ferrarochoi.com](http://www.ferrarochoi.com)The design team also included:
- Mechanical engineer
- Environmental building consultant
- Plumbing engineer
- Energy consultant
- Electrical engineer
- Lighting designer
Finance & Cost
With the exception of its signature photovoltaic array, HGEC was financed by the U.S. Department of Energy, administered through the State of Hawaii Department of Business, Economic Development, and Tourism.
The photovoltaic array and energy distribution system was funded in its entirety by the local utility, HELCO, in partnership with the Natural Energy Laboratory of Hawaii Authority, to increase public awareness of renewable and distributed energy systems.
- Equity: Government appropriation
Cost data in U.S. dollars as of date of completion.
- Total project cost (land excluded): $3,400,000
HGEC was conventionally funded. Therefore, the green aspects of the design (with the exception of the photovoltaic array and energy distribution system) came at no premium, and payback was immediate.
The main green strategy was eliminating the need for conventional air conditioning and ventilation by designing the entire building to function as a thermal chimney, providing both ventilation and cooling entirely by thermodynamics. With the exception of a small amount of energy required to pump deep seawater, no utility-provided energy is required for ventilation or cooling. Another cost-effective strategy was utilizing daylighting to eliminate the need for electric lighting during daytime hours.
Land Use & Community
The 6.5-acre HGEC site was selected for its visibility. It is the gateway to the Natural Energy Laboratory of Hawaii (NELH) campus, an 870-acre development along the south Kona coastline on the Big Island of Hawaii, at Keahole Point near the Kona International Airport. The HGEC site was established by the 1989 Hawaii Ocean Science and Technology (HOST) Park master plan.
Although designated urban, the HGEC site is essentially isolated from the nearest urban population in Kailua, approximately seven miles to the south. Since the Big Island has no public transportation system, access to the site must be via automobile despite its proximity to the primary coastal highway. Alternative transportation, including bicycles and electric vehicles, is used within the HOST/NELH development. NELHA staff often commute on site with battery-powered golf carts.
Approximately one-third of the HOST/NELH site has been developed. Density is moderate and typified by commercial tenants with various aquaculture businesses that utilize the deep seawater provided by NELHA.
The visitor complex, available to the community for outreach, demonstrations, and education, expresses traditional values within its state-of-the-art passive-solar design. Built on a platform similar to the Hawaiian heiau, the building shows respect for the region's habitat by using native coastal landscaping.
HGEC's visible presence along the highway was intended to spark interest in and renew dedication to accomplishing the State's goal of achieving independence from fossil fuels. (At the time the project was completed, 92% of Hawaii's energy came from imported oil.)
Responsible Planning
Ensure that development fits within a responsible local and regional planning framework
Support for Appropriate Transportation
- Provide safe access for bicyclers and pedestrians
Provide showers and changing areas for bicycle and pedestrian commuters
- Provide storage area for bicycles
- Provide access to public transportation
- Provide vehicle access to support car and vanpooling
- Provide incentives for non-automobile commuting options
- Provide for electric vehicle charging
Site Description
Approximately one-third of the site is natural pahoehoe lava terrain, 500 to 800 years old, covered by sparse patches of fire grass. This type of terrain, typical of undeveloped portions of the south Kona coastline, provides habitat primarily for coastal birds and insects. The project preserved 90% of this existing terrain. All landscaping consists of native, coastal plants that require little water.
State law requires all stormwater to be managed on site. Therefor, the parking area sheet drains to landscaping and rockscaping areas on either side.
- Lot size: 6.50 acres
- Previously undeveloped land
Water Conservation and Use
With an average annual rainfall of only 10 to 15 inches per year, harvesting precipitation is not viable, and additional potable water allocation to the area is not likely. Therefore, strategies for water conservation needed to be innovative.
Total water use for the project is 38,428 gallons per year inclusive of irrigation (11,856 gal/yr), toilet flushing (14,872 gal/yr), and sinks/drinking (11,700 gal/yr). However, potable water is not used for irrigation or toilet flushing. Instead, 20,280 gallons of condensation and 6,500 gallons of deep seawater are collected and used for these purposes annually.
Condensation is collected in a holding tank beneath the cooling coils that circulate 45°F seawater used to chill incoming air used for ventilation. A small amount of the deep seawater is diverted and collected with the condensation. The resulting mix is used for deep rooted plant irrigation and toilet flushing.
Shallow rooted plants are also irrigated by condensation, but in a different manner. A closed loop system piping is located immediately below the surface of shallow rooted plants. Seawater at 45°F circulates through the pipes, and condensation continuously forms on the pipe surfaces, irrigating coastal native plants that are suited to the environment and require minimal water.
The use of condensation in this way provides approximately 70% of the total facility water demand.
Indoors, the project team used low-flow fixtures throughout the building. Wastewater is treated in an on-site septic system and recharged into the aquifer.
Water Use
-
Indoor potable water use: 26,600 gal/yr (101,000 liters/yr)
Outdoor potable water use: 11,900 gal/yr (44,900 liters/yr)
- Total potable water use: 38,400 gal/yr (145,000 liters/yr)
Potable water use per unit area: 10.7 gal/sq ft (435 liters/sq meter)
Development Impacts
- Minimize development impact area
- Minimize building footprint
Waterless Fixtures
- Specify waterless urinals
Runoff Reduction
- Use planted swales instead of curbs and gutters
Landscape Plantings
- Landscape with indigenous vegetation
- Plant trees to shade parked vehicles
Managing Stormwater
- Utilize sheet flow
Construction Impacts
- Minimize soil erosion from construction activities
Integration with Site Resources
Integrate on-site wastewater treatment system with landscape design
Site Planning
- Protect and celebrate a site’s uniqueness
Energy
The building is designed to consume about 20% of the energy that would be required by a comparable building designed in minimal compliance with ASHRAE 90.1-1999.
A 20-kilowatt photovoltaic system takes advantage of high insolation to provide power. The system is expected to produce 24,455 kilowatt-hours of electricity annually. After an adjustment to the seawater pumping system in 2006, the building became a net-exporter of electricity; the photovoltaic system produces more energy than the building uses.
Passive thermal chimneys move air without mechanical equipment, allowing the design team to eliminate conventional air conditioning. The copper roof collects heat, which is radiated into an insulated ceiling plenum. The hot air rises up and out through actual chimneys, drawing cool replacement air into occupied space through an underfloor plenum connected to a fresh-air inlet between the multipurpose and administration buildings.
Cold, deep seawater, pumped from 3,000 feet below sea level, passively cools the building. The water, which arrives at 45°F, is distributed through cooling coils located in a dedicated air inlet structure. The cooled air then passes through a plenum beneath the buildings before rising through the buildings to exit at a high level. The only energy consumed for cooling is that used to run the seawater pump. NELHA provides the seawater to HGEC for $0.32 per thousand gallons.
The long axis of the building is oriented east-west for ideal shading and daylighting. There is no need for electric ambient lighting during daytime business hours (8:00 am to 6:00 pm) because the building is entirely daylit. When electric lighting is needed, fixtures are controlled by occupancy sensors and photosensors.
The building is well insulated for its climate. The mass walls have a U-value of 0.158, and R-11 batt insulation was added to the inside of the eight-inch concrete masonry unit walls. The assembly U-value for the fenestration is 1.1.
Materials & Resources
Locally manufactured construction materials used for HGEC include lava rock, concrete, and concrete masonry units. Although these materials did not meet LEED credit criteria for local materials, the production plants are located within 25 miles of the project, significantly reducing the energy embedded in their transportation. These materials are also inherently durable and should require no regular maintenance.
Construction materials with post-industrial or post-consumer recycled content include steel, thermoplastic olefin (TPO) roofing, copper roofing, thermal and acoustic insulation, gypsum board, carpet, resilient flooring, and countertops.
Indoor finishes emit low or no volatile organic compounds (VOCs). Carpet tile was used in lieu of glue-down carpet in the multipurpose space, and gravity-laid resilient flooring was used in the administrative areas.
A glass, paper, plastic, and metal recycling program is followed in the building.
HGEC is a small facility designed for ultimate flexibility. Predicted service life of the project is 50 years.
The multipurpose space supports a variety of activities, including exhibits, conferences, outreach, education, seminars, and community meetings. Raised-access flooring allows users to change the location of floor outlets and communications and data devices to suit various activities.
The administration area, which also features raised-access flooring, can be furnished with up to four workstations that can be rearranged.
Recyclable Materials
- Specify carpet from manufacturers who will recycle used carpet
Plan for Materials Longevity
- Use materials and systems with low maintenance requirements
Job Site Recycling
- Require a waste management plan from the contractor
- Set up labeled bins to keep recyclable materials separate
- Require that subcontractors keep their wastes separate
Recycling by Occupants
Specify recycling receptacles that are accessible to the occupants
Post-Consumer Recycled Materials
- Specify carpet tiles made with recycled-content backing
Pre-Consumer Recycled Materials
- Specify floor tiles with recycled content
- Use recycled-content rubber flooring
Transportation of Materials
Prefer materials that are sourced and manufactured within the local area
Indoor Environment
The quality of HGEC's indoor environment stems from excellent daylighting, views, ventilation, and thermal comfort.
During daytime hours, daylighting provides all necessary lighting. All of the occupied spaces offer substantial views, as virtually all of the south and north elevations feature glass, and all of this glass is shaded from direct sun. A translucent window treatment provides room darkening or privacy when desired.
Windows are fixed, as operable windows would interfere with the chimney effect. The ventilation design is based on stack ventilation. Cross ventilation was considered undesirable, as it would have introduced noise, wind, and dust.
The thermal chimney responds to interior and exterior heat gain, maintaining thermal comfort: when temperatures rise, the chimney effect strengthens and introduces more cool air to the building. The building maintains temperatures between 72°F and 76°F without mechanical controls. Ventilation rates range from 8 to 15 air changes per hour (ACH), exceeding health code requirements of 3 to 4 ACH. Ventilation is always 100% outside air. Outside air with 65% to 75% humidity loses moisture as it is drawn across the deep seawater cooling coils. Indoor humidity is maintained between 55% and 65%.
The contractor implemented an indoor air quality management plan during construction, and materials were selected for their low emissions of volatile organic compounds (VOCs).
Visual Comfort and The Building Envelope
Orient the floor plan on an east-west axis for best control of daylighting
Use large exterior windows and high ceilings to increase daylighting
Choose interior and exterior glazing to maximize daylight transmission
Visual Comfort and Interior Design
Select only white to midrange finishes to maximize reflectance of light
Acoustics and Occupant Noise
Specify acoustically absorbent materials to lower reflected noise levels
Reduction of Indoor Pollutants
- Specify zero-VOC interior latex paints
Pollutant Management During Construction
Store gypsum board during construction in a well-ventilated area
Ventilation During Construction
Provide adequate ventilation whenever construction activities are occurring in confined space
Building Commissioning for IEQ
Use a comprehensive commissioning process to ensure that design intent is realized
Facility Policies for IEQ
- Recommend a non-smoking policy for the building
Awards
- AIA/COTE Top Ten Green Projects in 2007
Ratings
Zero Energy Building
Energy and Atmosphere, 0 of 0 possible points
Net Zero Site Energy, Building produces at least as much energy as it uses in a year, when accounted for at the site.
Net Zero Source Energy, Building produces at least as much energy as it uses in a year, when accounted for at the source.
Net Zero Energy Emissions, Building produces at least as much emissions-free renewable energy as it uses from emission-producing energy sources annually.
Because of the aggressive energy efficiency design strategies and the 20-kilowatt photovoltaic (PV) system, the Hawaii Gateway Energy Center (HGEC) is a net zero energy building (ZEB) that actually exports electricity. HGEC employs extensive daylighting, a passive thermal chimney, and a cooling system that utilizes seawater to reduce energy consumption. More details about these features are available below and in the Energy section.
U.S. Green Building Council LEED-NC, v.2/v.2.1 in 2005; achievement level: Platinum (52 points)
Sustainable Sites, 9 of 14 possible points
- SS Prerequisite 1, Erosion & Sedimentation Control
- SS Credit 1, Site Selection
SS Credit 4.1, Alternative Transportation, Public Transportation Access
SS Credit 4.3, Alternative Transportation, Alternative Fuel Refueling Stations
- SS Credit 4.4, Alternative Transportation, Parking Capacity
SS Credit 5.1, Reduced Site Disturbance, Protect or Restore Open Space
- SS Credit 5.2, Reduced Site Disturbance, Development Footprint
- SS Credit 6.1, Stormwater Management, Rate and Quantity
- SS Credit 6.2, Stormwater Management, Treatment
- SS Credit 8, Light Pollution Reduction
Water Efficiency, 5 of 5 possible points
- WE Credit 1.1, Water Efficient Landscaping, Reduce by 50%
WE Credit 1.2, Water Efficient Landscaping, No Potable Water Use or No Irrigation
- WE Credit 2, Innovative Wastewater Technologies
- WE Credit 3.1, Water Use Reduction, 20% Reduction
- WE Credit 3.2, Water Use Reduction, 30% Reduction
Energy and Atmosphere, 17 of 17 possible points
- EA Prerequisite 1, Fundamental Building Systems Commissioning
- EA Prerequisite 2, Minimum Energy Performance
- EA Prerequisite 3, CFC Reduction in HVAC&R Equipment
EA Credit 1.1a, Optimize Energy Performance, 15% New 5% Existing
EA Credit 1.1b, Optimize Energy Performance, 20% New 10% Existing
EA Credit 1.2a, Optimize Energy Performance, 25% New 15% Existing
EA Credit 1.2b, Optimize Energy Performance, 30% New 20% Existing
EA Credit 1.3a, Optimize Energy Performance, 35% New 25% Existing
EA Credit 1.3b, Optimize Energy Performance, 40% New 30% Existing
EA Credit 1.4a, Optimize Energy Performance, 45% New 35% Existing
EA Credit 1.4b, Optimize Energy Performance, 50% New 40% Existing
EA Credit 1.5a, Optimize Energy Performance, 55% New 45% Existing
EA Credit 1.5b, Optimize Energy Performance, 60% New 50% Existing
- EA Credit 2.1, Renewable Energy, 5%
- EA Credit 2.2, Renewable Energy, 10%
- EA Credit 2.3, Renewable Energy, 20%
- EA Credit 3, Additional Commissioning
- EA Credit 4, Ozone Depletion
- EA Credit 5, Measurement and Verification
- EA Credit 6, Green Power
Materials and Resources, 4 of 13 possible points
- MR Prerequisite 1, Storage & Collection of Recyclables
- MR Credit 2.1, Construction Waste Management, Divert 50%
- MR Credit 2.2, Construction Waste Management, Divert 75%
MR Credit 4.1, Recycled Content: 5% (post-consumer + 1/2 post-industrial)
MR Credit 4.2, Recycled Content: 10% (post-consumer + 1/2 post-industrial)
Indoor Environmental Quality, 12 of 15 possible points
- EQ Prerequisite 1, Minimum IAQ Performance
- EQ Prerequisite 2, Environmental Tobacco Smoke (ETS) Control
- EQ Credit 1, Carbon Dioxide (CO2) Monitoring
- EQ Credit 2, Increase Ventilation Effectiveness
EQ Credit 3.1, Construction IAQ Management Plan, During Construction
EQ Credit 3.2, Construction IAQ Management Plan, Before Occupancy
- EQ Credit 4.1, Low-Emitting Materials, Adhesives & Sealants
- EQ Credit 4.2, Low-Emitting Materials, Paints
- EQ Credit 4.3, Low-Emitting Materials, Carpet
- EQ Credit 5, Indoor Chemical & Pollutant Source Control
- EQ Credit 7.1, Thermal Comfort, Comply with ASHRAE 55-1992
- EQ Credit 7.2, Thermal Comfort, Permanent Monitoring System
- EQ Credit 8.1, Daylight & Views, Daylight 75% of Spaces
- EQ Credit 8.2, Daylight & Views, Views for 90% of Spaces
Innovation and Design Process, 5 of 5 possible points
ID Credit 1.1, Innovation in Design "Exemplary Performance, WEc3"
ID Credit 1.2, Innovation in Design "Exemplary Performance, EAc1"
ID Credit 1.3, Innovation in Design "Exemplary Performance, EAc2"
ID Credit 1.4, Innovation in Design "Exemplary Performance, EAc6"
- ID Credit 2, LEED® Accredited Professional
Lessons Learned
Strong support and encouragement by the client as well as the whole-systems design process helped ensure the project's success. The general contractor was also engaged and proactive, which helped with the LEED submittal process.
Because the project was delivered on a design-bid-build basis, contractor input did not occur until the construction phase. Having contractor input earlier in the process would have helped the project team tackles issues of constructability, waste management, and value engineering.
Learn More
It is possible to visit this project. isits are possible, pending availability of staff. Send inquiries to [email protected].
Bill Brooks (Tour Contact) Ferraro Choi and Associates, Ltd. 733 Bishop Street, Suite 2620 Honolulu, HI 96813 808-533-8880 [http://www.ferrarochoi.com](http://www.ferrarochoi.com) *Primary Contact* William Brooks, AIA Ferraro Choi And Associates, Ltd. Architect 733 Bishop Street Suite 2620 Honolulu, HI 96813 808-540-0802 [http://www.ferrarochoi.com](http://www.ferrarochoi.com)