
Discovery Center at South Lake Union
|
|
|
|
|
|
Certifications & Awards
Project Team
- Architect: Miller-Hull Partnership
- Owner: Vulcan, Inc.
Green Building Audio
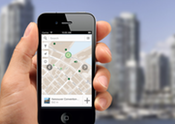
Our audio tours qualify.
Get one today!
Summary
This modular "pavilion in the park" was designed to be demountable and transportable for future disassembly and reassembly at multiple future locations. Its first use was for an exhibit telling the story of Seattle's South Lake Union neighborhood—its past, present, and future.
The project sits on the eastern edge of a full-block urban park that has been gifted to the city until the site is developed to its maximum zoning potential. As a temporary building, the structure sits lightly on the land, suspended above the gently sloping terrain atop short concrete piers. The building edges are cantilevered, allowing the grade and vegetation to run uninterrupted beneath.
Four-sided steel frame bents, bolted together, provide the structure for the building and span the interior gallery and exhibit space. The metal-clad building envelope components are designed as shop-fabricated, modular assemblies. The service functions of the pavilion are housed in a linear component that faces the park. Its softer wood materials and colors harmonize with the adjacent park and open space.
Presentation centers for residential developments such as this one typically have very short lifespans, since they disappear after construction is complete and the units sold. The modular nature of the project will allow it to serve for a much longer period of time. The building separates at three integrated joints to break into four separate modules capable of being transported along surface streets, where the building may resume functioning in its current capacity or be reprogrammed for an entirely new use.
Site Description
The building sits lightly on the land, preserving the sloping terrain through the use of cantilevered steel frames set on short concrete piers.
A form of a green area ratio factor, pioneered in Berlin, Germany, has been adopted by the City of Seattle as part of its zoning code. The Seattle Green Factor program calculates a score (a “green factorâ€) for a site based on the area of lawn or grass pavers, number and maturity of trees and bushes, area of green roofs and walls, and other strategies. Buildings must achieve a green factor of 0.30 or greater. The Discovery Center served as a case study project for the program, and achieved a green factor of 0.51.
Water Conservation and Use
The project utilizes a variety of techniques to manage stormwater runoff. Prior to construction of this facility, the site was a grass ball field with an existing stormwater detention tank. This tank was not large enough to handle added runoff from the building roof and paved areas, and a conventional design would suggest adding a new detention tank. The project team chose to use low-impact design strategies instead, slowing and filtering the stormwater on site so no new detention tanks were necessary.
Runoff from the roof is directed into a rain garden at the north end of the building, where deep biomitigative soils hold the water and allow it to evaporate. A rain garden along the edge of the asphalt parking lot serves the same function for runoff from the pavement and demonstrates the concept of "eco-street" frontage for urban areas. Much of the parking area uses a permeable paver system that allows rainwater to percolate into the ground. This approach decreased the peak runoff rate by an estimated 44% and the runoff volume by an estimated 37% for the design storm event, compared with a conventional building. The project team chose native and drought-tolerant plants to conserve water and provide wildlife habitat on site.
High-efficiency toilets and waterless urinals reduce the project's water use to just 45,000 gallons per year, a 15% reduction in internal water use, compared with a typical building of this type.
Energy
Important considerations were given to the design of the mechanical and electrical systems to facilitate the demountable nature of the building. The electrical, lighting, and mechanical systems are each contained within the 40-foot modules for practical disassembly and reassembly. For example, one small dedicated mechanical unit and associated supply and return ductwork is contained within each of the four modules, rather than having one system serve the whole building. The electrical system spans the whole building, but the main electrical conduit below the floor incorporates a disconnect junction box beneath each of the three separation joints so that only one electrical connection needs to be severed and reestablished when the building is disassembled and moved. The building uses air-source heat pumps to heat and cool the building.
For outdoor lighting, the project team chose high-efficiency electrodeless fluorescent lamps with a power consumption of 85 watts and a lamp life of 100,000 hours. Instead of lighting walkways from overhead, the team chose to use low-voltage lighting mounted low near walkway surfaces. Energy security
The thermally efficient building envelope, extensive daylighting, and natural ventilation allow the building to operate even in a blackout if required.
Materials & Resources
Several factors drove the selection of materials and design of assemblies, including durability, recycled content, and environmental responsibility. A primary goal was to design assemblies and select materials that would facilitate the required demountable aspect of the project.
The steel frames were designed to incorporate shop-welded rigid corner connections with splice plates and exposed bolted connections at the vertical components of the bents. All of the frame components were painted off site, then transported to the site, hoisted into place, and spliced together quickly and efficiently.
The roof framing system was designed with glued-laminated beam purlins at 4-feet on center, spanning 20 feet from frame-to-frame, with oriented-strand-board sheathing spanning perpendicularly across the purlins without the need for any intermediate joist framing. Exposed laminated-strand-lumber blocking conceals the sheathing joints and provides the required edge for nailing. This approach allowed the roof system to be fabricated, sealed, and stained off site in 8-foot by 20-foot sections, which were then transported to the site and hoisted into place with a crane.
Environmentally responsible materials included 500 cubic yards of recycled concrete used as sub-base at the parking area; concrete containing flyash (50% at footings and piers and 30% at exposed slabs); composite decking planks with recycled content at exterior decking areas; paper-based countertops, partitions, and exhibit display casework; oriented-strand board and laminated-strand lumber; linoleum; and carpet with recycled content.
Diversion of Construction & Demolition Waste
The contractor employed strategies for reducing and recycling construction waste materials and achieved a 97% diversion rate for all construction waste leaving the site.
Green Products Used
Design for Adaptability to Future Uses
The primary program requirement of the project was to provide a flexible and adaptable interior exhibit space in a building that could be separated, moved, and reconnected.
The flexibility of the interior has allowed a significant portion of the exhibit space to be refitted since its initial construction to present a new series of residential communities coming on-line.
The contractor was involved during the design process to confirm the requirements for moving the building in the future. Module size constraints for street transport were identified, and joint connection designs were developed to ensure the future relocation would be successful.
The building employs three disconnect joints to break the structure into four modules, each 40 feet wide and 73 feet long. All interior and exterior finishes and assemblies have a built-in joint at this break point, covered by a removable plate, cap, or coping to suit each surface or location. This demountable aspect of the building is demonstrated to the public at the interior through the use of narrow aluminum closure plates on the floor and wall surfaces where they cross the disconnect joints. Barrier-free access to the main entrance and the catering kitchen is maintained by incorporating gangway ramps with integrated hinged joints, allowing the ramps to adapt to the topography of future building locations.
Awards
AIA, Top Ten- 2008