CBF Merrill Environmental Center
|
|
|
|
|
|
|
|
|
|
|
|
Certifications & Awards
- LEED-NC v.1.0 in 2000 achievement level Platinum
- Green Building Challenge in 2002 achievement level 2.7 in GB Tool 1.76
Project Team
- Owner: The Chesapeake Bay Foundation Inc.
Green Building Audio
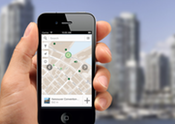
Our audio tours qualify.
Get one today!
Summary
The Chesapeake Bay Foundation, an environmental advocacy, restoration, and education organization, is headquartered in Annapolis, Maryland.
**This building was originally imported from the U.S. Department of Energy Energy Efficiency and Renewable Energy
Building Technologies Database (http://eere.buildinggreen.com/overview.cfm?projectid=69) on 2009-06-06. Please confirm that the import was successful, login, and remove this message. Help make the Green Building Brain better.**
Overview
- Location: Annapolis, MD
- Building type(s): Interpretive Center, Commercial office
- New construction
- 32,000 sq. feet (2,970 sq. meters)
- Project scope: 2-story building
- Suburban setting
- Completed December 2000
Rating: U.S. Green Building Council LEED-NC, v.1.0--Level: Platinum
Rating: Green Building Challenge --Level: 2.7 in GB Tool 1.76
The Chesapeake Bay Foundation, an environmental advocacy, restoration, and education organization, is headquartered in Annapolis, Maryland.
Environmental Aspects
The Chesapeake Bay Foundation Headquarters building is recognized as one of the "greenest" buildings ever constructed. Sustainability issues ranging from energy use to material selection were given serious consideration throughout design and construction of this facility. It was the first building to receive a Platinum rating through the U.S. Green Building Council's LEED (Leadership in Energy and Environmental Design) Rating System, version 1.0.
Owner & Occupancy
Owned and occupied by The Chesapeake Bay Foundation Inc., Corporation, nonprofit
- Typically occupied by 80 people, 40 hours per person per week
This conventional office environment is open 8:30 AM to 5:30 PM. Weekend and evening functions are occasionally held at the Center.
Building Programs
Indoor Spaces: | Office (65%), Conference (10%), Mechanical systems (9%), Lobby/reception (4%), Circulation (4%), Restrooms (3%), Electrical systems (3%), Dining (2%) |
Outdoor Spaces: | Restored landscape (48%), Wildlife habitat (40%), Parking (5%), Interpretive landscape (2%), Drives/roadway (2%), Pedestrian/non-motorized vehicle path (2%), Patio/hardscape (1%) |
Keywords
Integrated team, Design charrette, Training, Green specifications, Commissioning, Operations and maintenance, Transportation benefits, Open space preservation, Wildlife habitat, Wetlands, Indigenous vegetation, Stormwater management, Water harvesting, Efficient fixtures and appliances, Drought-tolerant landscaping, Graywater, Wastewater treatment, Massing and orientation, Insulation levels, Glazing, Airtightness, Passive solar, HVAC, Lighting control and daylight harvesting, Efficient lighting, On-site renewable electricity, Benign materials, Salvaged materials, Recycled materials, Local materials, Certified wood, C&D waste management, Occupant recycling, Daylighting, Natural ventilation, Ventilation effectiveness, Noise control, Low-emitting materials
Team & Process
The U.S. Green Building Council's LEED Rating System was used in setting goals for the project before the design commenced. Benchmarking tours of other green projects and CBF's educational centers were influential in the design.
A peer review of the concept design was organized by the Sustainable Building Industries Council (funded by the Department of Energy) and included reviewers from the Maryland Energy Administration, Maryland Department of Natural Resources, World Wildlife Fund and National Renewable Energy Laboratory. An integrated approach to design was used, and in-house engineers worked closely with architects.
Construction administration was performed by the team architect already familiar with the design and project goals. The contractor did not have a lot of experience with the building systems and the green process, and the project might have benefited if the contractor shared the client's goals.
The owner used the design team, rather than an independent third-party, as Commissioning Agent. As a result, the contractor felt that the Commissioning Agent could not be a neutral arbiter. The contractor had a difficult time understanding the intent of commissioning systems as opposed to testing individual pieces of equipment.
CBF has done extensive work with the National Renewable Energy Laboratory (Department of Energy National Laboratory) to evaluate the performance of the building in terms of energy and resource efficiency.
An in-depth post-occupancy evaluation of human factors in the building was published in April, 2005. An online survey and in-person interviews of Merrill Center occupants were used to collect the information. The online survey tool used is from the Center for the Built Environment at the University of California at Berkeley. A report summarizing the results is available (see the "Learn More" screen).
Key findings from the Occupant Indoor Environmental Quality survey, interviews and discussion groups are as follows:
Occupants were highly satisfied with the Merrill Center building as a whole. In fact, the score for overall building satisfaction was the second highest in the entire CBE survey database.
Satisfaction with air quality was also very positive and represents the highest level of air quality satisfaction in the CBE database.
Close to 90% of the occupants were also satisfied with daylighting, the overall amount of light, and access to views.
Ratings for the psychosocial outcomes were also positive, with about 80% of the occupants experiencing high levels of morale, well being and sense of belonging at work.
Occupants have a strong sense of pride in the building, as indicted by the fact that 97% of survey respondents said they were proud to show the office to visitors.
Acoustical conditions were the most negatively rated, primarily due to distractions from people talking and loss of speech privacy associated with the highly open environment. Even so, the acoustics score was well above average in comparison with the CBE database.
Findings from the interviews and focus groups also provide additional insights about the psychosocial benefits of the building. Psychological benefits included sense of pride in the values conveyed by the building, a more positive overall workplace experience, and a strong connection to the natural environment. Social benefits included improved communication and sense of belonging as well as feelings of being treated in an egalitarian manner, especially regarding access to benefits of daylight and views.
Participants in the interviews and focus groups also felt that the building very strongly conveyed the mission and values of the Foundation. As one senior executive pointed out, the building’s location on the edge of Chesapeake Bay allows everyone to “see what we are working on and what we are working for.â€
A content analysis of the interviews and discussion groups showed that 74% of the comments were of a positive nature, and 27% were about concerns or problems. The most frequently cited concerns were temperature conditions, noise distractions, insufficient meeting rooms, and glare from windows. The most frequently cited positive factors were the connection to nature and the Bay, the access to daylight and views, the openness of the space, the lunch room, and the overall aesthetics of the building.
Designing Low-Energy Buildings with Energy-10 (DLEB/E-10) software was used for energy analysis.
The design team also included:
- Plumbing engineer
- Commissioning agent
- Mechanical engineer
- Interior designer
- Environmental building consultant
- Electrical engineer
Finance & Cost
Funds for the building were raised through a special building campaign and private donations. No money came from regular membership revenues. The total outlay for the building over the term of its loan is less than the client would pay in rent for a similarly sized facility. The total cost for the project, including land acquisition, savings from easements, and the sale of existing properties, is $11.6 million.
- Procurement process: Design-bid-build
Cost data in U.S. dollars as of date of completion.
- Total project cost (land excluded): $7,500,000
Some of the hard costs:
- construction: $199 per sq foot ($2,140 per sq meter)
Of the $199/ft2 cost for building construction, roughly $46/ft2 are directly attributable to premiums spent for green measures. This initial investment will pay for itself within 7-8 years through reduced operations costs.
Land Use & Community
To encourage responsible methods of transportation in its work force, and specifically to decrease the amount of nitrogen oxides washing into the Chesapeake Bay, the Foundation has implemented incentives for staff to bicycle or carpool to work. Bike racks, showers, and changing rooms are available for bikers, walkers, and runners. Free battery charging encourages the use of electric cars. The Center also owns and makes available bicycles and a hybrid car. Finally, amenities such as videoconferencing and telecommuting connections, as well as breakfast and lunch facilities, are available on-site.
Property Evaluation
Assess property for integration with local community and regional transportation corridors
Properties with Excessive Impacts
- Avoid contributing to sprawl
- Avoid developing prime agricultural land
- Avoid building on a flood-prone property
Support for Appropriate Transportation
Provide showers and changing areas for bicycle and pedestrian commuters
- Provide storage area for bicycles
- Provide incentives for non-automobile commuting options
- Provide for electric vehicle charging
Property Selection Opportunities
- Select already-developed sites for new development
Site Description
Site and water were given special consideration at the Foundation Headquarters.
The building was sited in a manner consistent with Maryland's Smart Growth criteria, on the footprint of the existing buildings. Some existing pavement was removed as parking space was moved underground, resulting in an increase in pervious surface.
Native landscaping is important to the organization, and habitats ranging from wetlands to an oyster reef are currently being restored on-site.
The center captures and reuses rainwater and uses a bioretention filter to treat oil and other pollutants in runoff from the pervious parking area.
Efforts were made through landscaping and exterior material choices to minimize the heat island potential of the project. Additionally, light pollution is minimized by the use of timers on exterior lights.
The center employs composting toilets in place of conventional flush toilets. When combined with other water-efficient appliances and native landscaping, the result is a 90+% reduction in water use over an otherwise comparable conventional office building.
- Lot size: 31.50 acres
- Building footprint: 13,700 sq ft (1,270 sq meters)
Wetlands, Sensitive habitat, Preexisting structure(s), Previously developed land, Lake/pond, Running water, Previously undeveloped land
Water Conservation and Use
Water Use
- Indoor potable water use: 22,000 gal/yr (83,300 liters/yr)
- Outdoor potable water use: 0 gal/yr (0 liters/yr)
-
Potable water use per occupant: 275 gal/person/yr
(1,040 liters/person/yr)
Ecosystem Restoration
- Replant damaged sites with native vegetation
Waterless Fixtures
- Use composting toilets
Runoff Reduction
- Use planted swales instead of curbs and gutters
- Install gravel paving in a matrix to retain permeability
Landscape Plantings
- Landscape with plants that provide wildlife forage or habitat
- Plant trees to shade parked vehicles
Low-Water-Use Fixtures
- Use automatic faucet controls for lavatories
Managing Stormwater
Design a constructed wetland for pollutant removal from stormwater
Rainwater Collection
- Collect and store rainwater for uses in building
Demand for Irrigation
- Select plants for drought tolerance
Energy
Energy issues were considered in the design of the Headquarters. The building was sited in order to take advantage of southern solar exposure as well as prevailing winds for natural ventilation. Daylighting is emphasized by large windows, clerestories, and an open interior design.
The south wall of the center uses photovoltaic panels to produce energy on-site. Solar panels on the roof heat water for indoor use. Geothermal wells are used for heating in the winter and cooling in the summer.
A sophisticated total energy management system monitors and controls energy use in the building. The system alerts employees when windows should be opened. Other windows are opened and closed automatically. The system also monitors daylight levels, adjusting electric lighting as needed.
Materials & Resources
In construction, the building incorporated a "cradle-to-cradle" rather than "cradle-to-grave" philosophy. This philosophy requires consideration of all materials not only for what they are made of, but what they can be made into at the end of their useful lives.
All existing structures on the construction site were recycled (concrete from original foundations is now being used as road bed fill, for example). Materials were selected for recycled content (galvanized siding made from cans, cars, and guns; interior fabrics; and rubber flooring). Likewise, materials from renewable or regenerable resources were incorporated (cork flooring comes from the bark of the cork oak tree which can be harvested without killing the tree and regenerates in 7 to 9 years). All wood was from renewable resources (the main foyer's bamboo flooring is harvested from plants that regrow in approximately 3 years).
Roof and wall enclosures use Structurally Insulated Panels (SIPS). These use high R-value insulating foam in place of conventional wood studs and rafters, resulting in a high performance building envelope using a fraction of the wood of conventionally framed structures. Parallel strand timber beams from new growth trees, harvested and quickly regenerated, provide timber stronger than conventional wood. More than 50 percent of the building materials came from a 300-mile radius to reduce environmental costs associated with travel.
Existing structures on the site were deconstructed rather than demolished and all materials were auctioned, salvaged, or recycled. The existing foundations were chipped and used as road base. Seven loads of chipped concrete were hauled off-site to be reused. With regard to construction waste, all cardboard, metals, concrete, cmu, asphalt, and land-clearing debris were recycled.
- Composting Toilets
- Cork Flooring
- Granulated Linoleum-Cork Composite Sheets
- High-Performance Fiberglass Windows
- Natural Linoleum Flooring
- Occupancy Sensors and Controls
- Photovoltaic Collectors
Recycled-Wood Fiberboard and Particleboard
Building Deconstruction
- Recycle materials to be discarded from existing structure
Design for Materials Use Reduction
- Consider exposing structural materials as finished surfaces
Job Site Recycling
- Require a waste management plan from the contractor
Toxic Upstream or Downstream Burdens
Use wood treated with less-toxic preservatives than the standard CCA or ACZA
- Use natural cork flooring
Resource-Efficient and Biobased Materials
Use engineered wood products in place of large-dimension timbers
Post-Consumer Recycled Materials
- Use plastic toilet partitions made from recycled plastic
Pre-Consumer Recycled Materials
- Prefer roofing materials with high levels of recycled content
Salvaged Materials
- Use salvaged wood for finish carpentry
Transportation of Materials
Prefer materials that are sourced and manufactured within the local area
Indoor Environment
Natural ventilation is used whenever possible, made more effective by a carbon dioxide monitor and automatically controlled operable windows. Additionally, efforts were made to limit the amount of toxic materials introduced to the indoor environment in the first place. VOC-free paints joined natural materials such as cork, linoleum, and bamboo in an effort to create a healthy working environment.
The building design incorporates extensive daylighting and appropriate shading as well as views of the Chesapeake Bay to maximize the visual comfort of employees.
Entry of Pollutants
Design entry to facilitate removal of dirt before entering building
- Avoid carpet and other hard-to-clean floor surfaces near entry
Visual Comfort and Interior Design
Design open floor plans to allow exterior daylight to penetrate to the interior
Ventilation and Filtration Systems
- Provide occupants with access to operable windows
Below Grade Rainwater and Groundwater
- Raise the building up on piers
Reduction of Indoor Pollutants
- Use only very low or no-VOC paints
- Specify prefinished wood or bamboo flooring
- Avoid wood products made with urea-formaldehyde binder
Building Commissioning for IEQ
Use a comprehensive commissioning process to ensure that design intent is realized
Maintenance for IEQ
Design isolated storage closet for cleaning and maintenance products
Awards
ASHRAE Technology Award in 2001; Category/title: National Capital Chapter 1st Place Award in the Commercial New division
- AIA/COTE Top Ten Green Projects in 2001
- Business Week/Architectural Record Awards in 2001
AIA Washington, D.C., Chapter in 2001; Category/title: Award for Excellence in Architecture
NESEA Green Building Awards in 2003; Category/title: First Prize: Places of Work
Building Design & Construction Magazine in 2001; Category/title: Grand Award, Building Team Project of the Year
Ratings
U.S. Green Building Council LEED-NC, v.1.0 in 2000; achievement level: Platinum
Planning Sustainable Sites, 7 of 11 possible points
- SS Credit 1, Landscaping for Erosion Control
- SS Credit 2.1, Reduced Heat Islands, Implement 1 or 2 Measures
- SS Credit 4, Reduce Habitat Disturbance
- SS Credit 5, Site Preservation/Restoration
SS Credit 7.1, Alternative Transit Facilities, Implement 1 or 2 Measures
SS Credit 7.2, Alternative Transit Facilities, Implement All 3 Measures
- SS Bonus Credit 1, Alternative Fueling Facilities
Improving Energy Efficiency, 7 of 11 possible points
- EA Prerequisite 1, Building Commissioning
- EA Prerequisite 2, Energy Efficiency
- EA Credit 1.1a, Energy Efficiency Level 1
- EA Credit 1.2a, Energy Efficiency, Level 2
- EA Credit 1.3a, Energy Efficiency, Level 3
- EA Credit 1.4a, Energy Efficiency, Level 4
- EA Credit 1.5a, Energy Efficiency, Level 5
- EA Credit 3, Waste Heat Recovery
- EA Credit 4.1, Renewable/Alternative Energy, 10%
Conserving Materials and Resources, 7 of 12 possible points
- MR Prerequisite 1, Elimination of CFCs
- MR Prerequisite 2, Storage & Collection of Recyclables
- MR Credit 2.1, Resource Reuse, Specify 5%
- MR Credit 3.1, Recycled Content, Level 1
- MR Credit 4.1, Construction Waste Management, Level 1
- MR Credit 4.2, Construction Waste Management, Level 2
- MR Credit 5, Local Materials
MR Credit 6.1, Elimination of CFCs & Halons, Mechanical Equipment
- MR Credit 7, Occupant Recycling
Enhancing Indoor Environmental Quality, 5 of 7 possible points
- IEQ Prerequisite 1, Elimination and Control of Asbestos
- IEQ Prerequisite 2, Indoor Air Quality
- IEQ Prerequisite 3, Smoking Ban
- IEQ Prerequisite 4, Thermal Comfort
- IEQ Credit 2.1, Low VOC Materials, Comply with 1 or 2 Items
- IEQ Credit 2.2, Low VOC Materials, Comply with All 3 Items
- IEQ Credit 3, Permanent Air Monitoring
- IEQ Credit 4, Chemical Storage Areas
- IEQ Credit 5, Architectural Entryways
Safeguarding Water, 6 of 8 possible points
- WE Prerequisite 1, Water Conservation
- WE Prerequisite 2, Elimination of Lead
- WE Credit 1, Water-Conserving Fixtures
- WE Credit 2, Water Recovery System
- WE Credit 4, Water-Efficient Landscaping
- WE Credit 5, Surface Runoff Filtration
- WE Credit 6, Surface Runoff Reduction
- WE Bonus Credit 2, Measurement and Verification
Improving the Design/Build Process, 1 of 1 possible points
- ID Bonus Credit 1, LEED® Accredited Professional
CBF Merrill Environmental Center achieved additional "Innovation in Design" credits for "Low Water Use" and "Exceptional Energy Measures".
Green Building Challenge in 2002; achievement level: 2.7 in GB Tool 1.76 The Green Building (GB) Tool is an Excel 2000 spreadsheet building assessment tool, designed by the International Initiative for a Sustainable Built Environment (iiSBE). The research tool is still being revised/updated, and is primarily used for assessing buildings entered in the Green Building Challenge. The tool provides a relatively accurate result for a wide range of occupancy type buildings. Scoring is based on a -2 to 5 point scale, comparing the building to an industry standard benchmark.
The project was assessed using the GB Tool 1.8 and received the following scores:
Total Score for Resources, Loadings, and IEQ: 2.7.
Performance Scores: Resources, 3.9; Loadings, 2.0; IEQ, 2.2; Service Quality, 3.5; Economics, 2.6; Management, 4.5.
Lessons Learned
The project's primary goal was to lead by example and to encourage sustainable development within the Mid-Atlantic region. The Center hosts several tours each week during which groups of architects, government officials, developers, contractors, students, and environmentalists from around the world witness the building's aggressive environmental strategies in action. The Center has been the focus of numerous research studies, including a study from the Massachusetts Institute of Technology on the viability of Natural Ventilation in the Mid-Atlantic region of the United States; a study on the effects of Indoor Environmental Quality on worker productivity; and continuous monitoring by the U.S. National Renewable Energy Laboratory.
Learn More
It is possible to visit this project and tours are available. The Philip Merrill Environmental Center (the Chesapeake Bay Foundation Headquarters) is located at 6 Herndon Avenue in Annapolis, MD.
A map and detailed directions from various locations are available online.
Contact the Chesapeake Bay Foundation to arrange a guided tour.
A virtual tour is available online.
The Chesapeake Bay Foundation (Tour Contact) 6 Herndon Avenue Annapolis, MD 21403 410-268-8816 [http://www.cbf.org](http://www.cbf.org)s
Analysis of the Energy Performance of the Chesapeake Bay Foundation
Magazines
“Good Design – And Good Businessâ€
Publication: Business Week (11/5/2001)“Resting Lightly on the Land – Novel Materials and Exceptional Teamwork Give Birth to the World’s Greenest Office Buildingâ€
Publication: Building Design & Construction (June 2001)A Deeper Shade of Green by Zachman, Will
Publication: Environmental Design & Construction (January/February 2000)LEEDing the Way
Publication: Landscape Architecture (May 2001)Lessons Learned - High-Performance Buildings by Torcellini, Paul; Judkoff, Ron; Crawley, Dru
Publication: ASHRAE Journal Vol. 46, No.9 p. S4 (September 2004)
Article describes lessons learned from six high-performance buildings: Oberlin College Lewis Center, OH; Zion Visitor Center, UT; BigHorn Home Improvement Center, CO; NREL Thermal Test Facility, CO; Cambria Office Building, PA; and Chesapeake Bay Foundation, MD. http://www.ashrae.orgThe Green Machine by McKee, Bradford
Publication: Architecture Magazine (2/1/2001)The Greenest Building in the Nation by Bonda, Penny
Publication: Interiors & Sources Magazine (Spring 2001)The Greenest Office on the Bay
Publication: Architectural Record (October 2001)
Web sites
Others
Technical Report: Analysis of the Energy Performance of the Chesapeake Bay Foundation's Philip Merrill Environmental Center by Griffith, B.; Deru, M.; Torcellini, P.
Publication: NREL/TP-550-34830 (4/2005)
As part of its evaluation for the U.S. Department of Energy, the National Renewable Energy Laboratory (NREL) published this detailed case study of the energy performance of the CBF Merrill Environmental Center comparing measured energy use to the project's design goals and identifing successes and lessons learned. (PDF 2.90 MB) Download Acrobat ReaderConference paper: Lessons Learned from Field Evaluation of Six High-Performance Buildings by Torcellini, Paul; Dru, Crawley; Shanti, Pless, et al. (July 2004)
NREL conference paper published for the 2004 ACEEE Summer Study on Energy Efficiency in Buildings. (PDF 716 KB) Download Acrobat ReaderReport: The Human Factors of Sustainable Building Design: Post Occupancy Evaluation of the Philip Merrill Environmental Center, Annapolis, MD by Heerwagen, Ph.D., Judith; Zagreus, Leah
Report summarizing the results of an online post-occupancy evaluation survey and in-person interviews of Merrill Center occupants. The online survey tool used is from the Center for the Built Environment at the University of California at Berkeley. The report was prepared for Drury Crawley at the U.S. Department of Energy's Building Technology Program. (PDF 443 KB) Download Acrobat ReaderBrochure: The Philip Merrill Environmental Center: Chesapeake Bay Foundation (April 2002)
Part of the U.S. Department of Energy's "Highlighting High Performance" series, this brochure is available online in PDF form. (PDF 679 KB) Download Acrobat Reader